Introduction
Refractory ceramics are non-metallic materials designed to withstand extreme temperatures (typically above 1,000°C) while maintaining structural and chemical integrity. Their unique properties make them indispensable in industries where high heat, thermal shock, and corrosive environments are prevalent.
Key Characteristics of Refractory Ceramics
High Melting Point
Refractory ceramics are engineered to endure extreme temperatures, often exceeding 1,600°C, with some advanced types (e.g., zirconia, silicon carbide) capable of withstanding 2,500°C or higher. This exceptional property makes them indispensable in industries where high-temperature processes are routine. Below is a detailed breakdown of why these materials have such high melting points and their industrial significance.
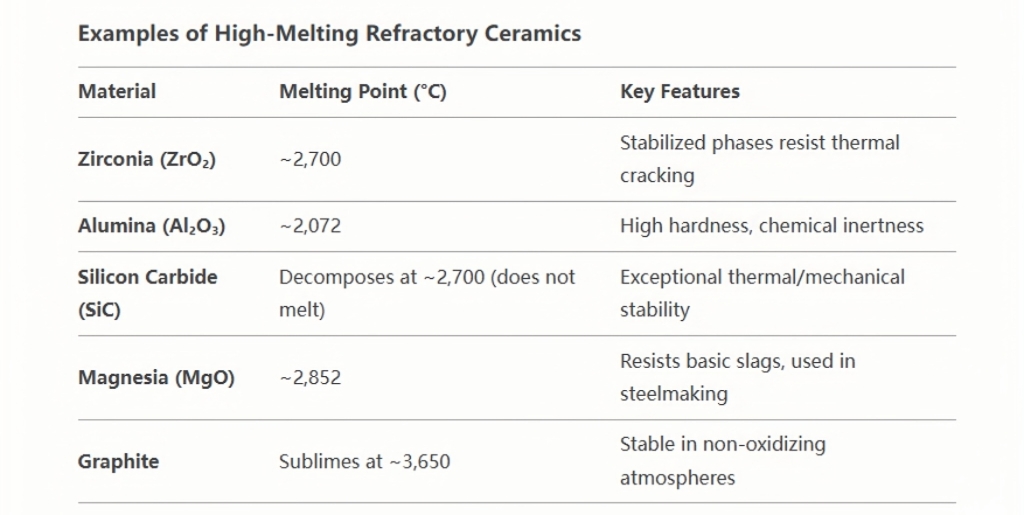
- Withstand temperatures exceeding 1,600°C, with some (e.g., zirconia) enduring up to 2,500°C.
- Enables use in environments like steelmaking furnaces.
Factors Contributing to High Melting Points
Strong Atomic Bonding
- Covalent/Ionic Bonds: Refractory ceramics are held together by strong covalent or ionic bonds (e.g., SiC, Al₂O₃), which require immense energy to break.
- Bond Strength: Higher bond dissociation energy directly correlates with higher melting temperatures.
Crystal Structure
- Dense, ordered crystalline lattices (e.g., alumina’s hexagonal structure, zirconia’s cubic/tetragonal phases) resist atomic rearrangement at high temperatures.
- Stabilized zirconia (e.g., yttria-stabilized ZrO₂) maintains structural integrity even near its melting point (~2,700°C).
Chemical Inertness
- High-purity ceramics (e.g., fused silica, magnesia) lack impurities that could lower melting points by creating weak spots.
- Non-reactive with molten metals, slags, or gases, preventing degradation.
High Purity and Dopants
- Pure oxides (e.g., Al₂O₃, MgO) avoid low-melting eutectic phases.
- Dopants like chromium or rare earths enhance thermal stability without compromising melting points.
Role of High Melting Points in Industrial Applications
Steelmaking and Metal Processing
- Blast furnaces, ladles: Alumina and magnesia linings withstand molten iron (~1,500°C) and slag.
- Crucibles: Graphite or zirconia crucibles melt metals like platinum (~1,768°C).
Glass Manufacturing
Melting tanks: Zirconia-corundum refractories resist molten glass (~1,600°C) without dissolving.
Aerospace and Defense
Rocket nozzles/heat shields: SiC and zirconia endure hypersonic re-entry temperatures (>2,000°C).
Cement Kilns
Silicon carbide linings survive clinker formation at ~1,450°C.
Nuclear Reactors
Uranium dioxide (UO₂) fuel pellets and zirconia cladding tolerate fission temperatures (>2,000°C).
Conclusion
The high melting points of refractory ceramics stem from their atomic bonding, crystal structure, and chemical purity. These properties enable their use in critical industries such as metallurgy, aerospace, and energy, where failure at high temperatures is not an option. Ongoing research aims to push these limits further, unlocking new applications in extreme environments.
Thermal Shock Resistance
Thermal shock resistance refers to a material’s ability to withstand rapid temperature changes without cracking or fracturing. For refractory ceramics, this property is critical in applications such as furnace linings, glass manufacturing, and aerospace components, where sudden heating or cooling cycles are common. Below is a detailed exploration of the mechanisms, influencing factors, and real-world relevance of thermal shock resistance in refractory ceramics.
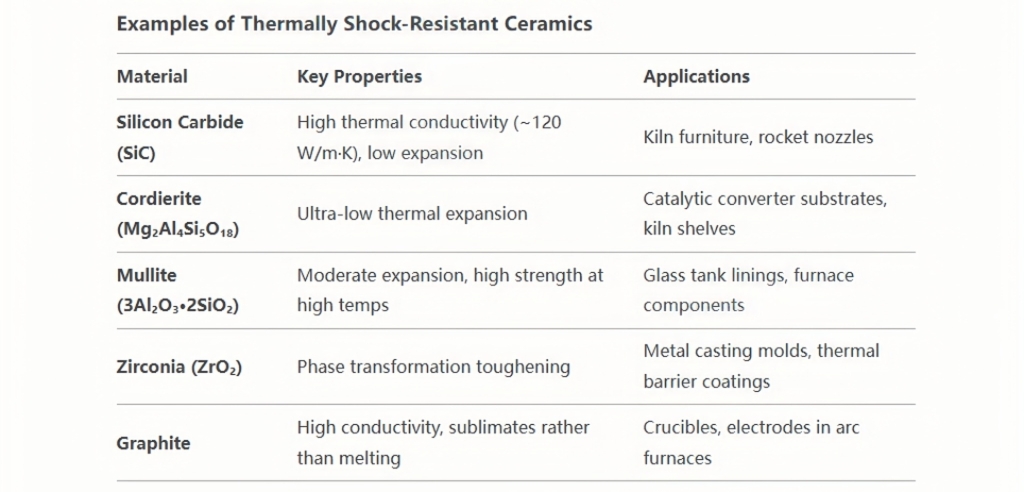
- Resist cracking during rapid temperature changes (e.g., glass manufacturing cycles).
- Achieved through low thermal expansion or composite structures.
Thermal shock resistance in refractory ceramics is achieved through a balance of low thermal expansion, high conductivity, and microstructural engineering. These materials enable technologies ranging from clean energy to space exploration, where rapid thermal cycling is unavoidable. Ongoing advances in composites and manufacturing promise to expand their capabilities, ensuring reliability in even more extreme environments.
Chemical Stability of
Bond Strength and Crystal Structure:
- Covalent/Ionic Bonding: Strong atomic bonds (e.g., Si-C in silicon carbide, Al-O in alumina) resist chemical attack.
- Dense Crystalline Phases: Materials like zirconia (ZrO₂) or magnesia (MgO) lack open channels for corrosive agents to penetrate.
Chemical Inertness:
- High-Purity Oxides: Alumina (Al₂O₃), silica (SiO₂), and zirconia (ZrO₂) are inherently unreactive with many molten metals and slags.
- Non-Oxide Ceramics: Silicon carbide (SiC) and silicon nitride (Si₃N₄) resist acidic and reducing environments but may oxidize in air at high temperatures.
Environmental Compatibility:
- Acid vs. Base Resistance:
- Acidic Slags: Silica (SiO₂) and alumina (Al₂O₃) perform well in acidic conditions (e.g., glass melts).
- Basic Slags: Magnesia (MgO) and doloma (MgO-CaO) resist alkaline environments (e.g., steelmaking slags).
- Oxidation Resistance: Non-oxide ceramics (e.g., SiC, graphite) require protective atmospheres or coatings to prevent oxidation.
Microstructural Design:
- Low Porosity: Dense ceramics minimize penetration of corrosive liquids or gases.
- Composite Systems: Adding secondary phases (e.g., chromium oxide to alumina) enhances slag resistance by forming protective layers.
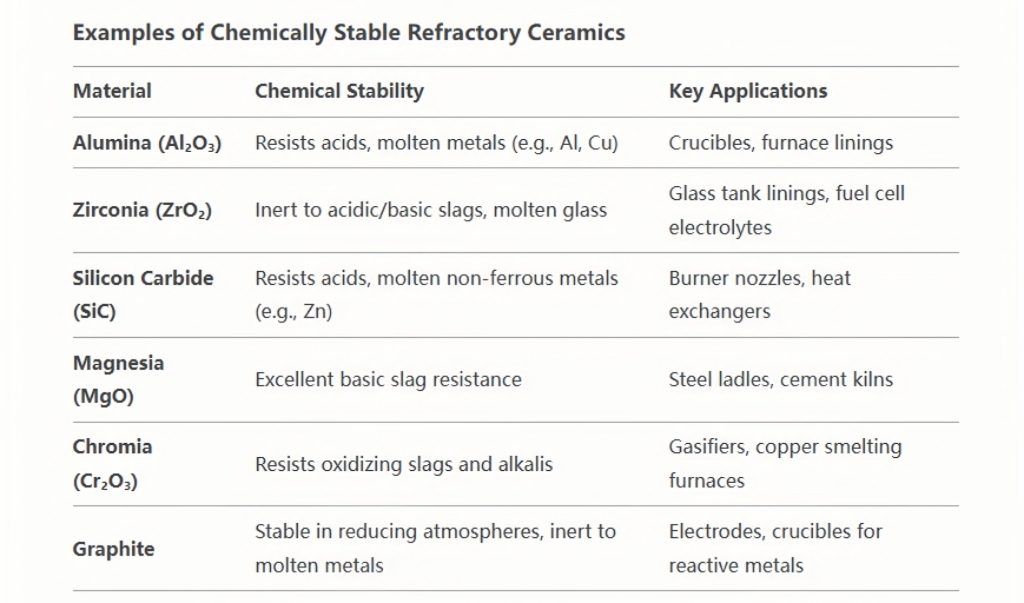
Chemical stability in refractory ceramics is governed by atomic bonding, phase composition, and microstructural design. These materials enable critical processes in extreme environments, from molten metal handling to toxic waste disposal. While challenges like slag penetration and oxidation persist, advances in composites and nanotechnology are driving the development of ceramics that combine chemical inertness with mechanical robustness. Their role in sustainable industries—such as clean energy and recycling—highlights their enduring importance in modern engineering.
Mechanical Strength at High Temperatures
Mechanical strength at elevated temperatures is a defining property of refractory ceramics, enabling their use in extreme environments where structural integrity under load is critical. Unlike metals or polymers, refractory ceramics retain their strength even at temperatures exceeding 1,000°C, making them indispensable in industries such as metallurgy, aerospace, and energy. Below is a detailed exploration of the mechanisms, influencing factors, and applications of high-temperature mechanical strength in refractory ceramics.
Bonding and Crystal Structure:
- Covalent/Ionic Bonds: Strong atomic bonds (e.g., Si-C in silicon carbide, Al-O in alumina) resist deformation.
- Crystalline Order: Dense, stable crystal lattices (e.g., hexagonal Al₂O₃, cubic ZrO₂) minimize dislocation movement, a key cause of plastic deformation.
Creep Resistance:
- Grain Boundary Engineering: Fine-grained ceramics (e.g., hot-pressed Si₃N₄) reduce grain boundary sliding, a primary creep mechanism.
- Secondary Phases: Additives like yttria (Y₂O₃) in zirconia or MgO in alumina form glassy phases that fill grain boundaries, inhibiting creep.
Thermal Stability:
- Phase Transitions: Materials like partially stabilized zirconia (PSZ) use phase transformations to absorb stress without fracturing.
- Oxidation Resistance: Non-oxide ceramics (e.g., SiC, Si₃N₄) form protective oxide layers (SiO₂) that slow further degradation.
Composite Design:
- Fiber Reinforcement: Carbon or SiC fibers in ceramic matrices (e.g., C/SiC composites) enhance fracture toughness and load-bearing capacity.
- Dispersion Strengthening: Nanoparticles (e.g., TiC in Al₂O₃) hinder crack propagation.
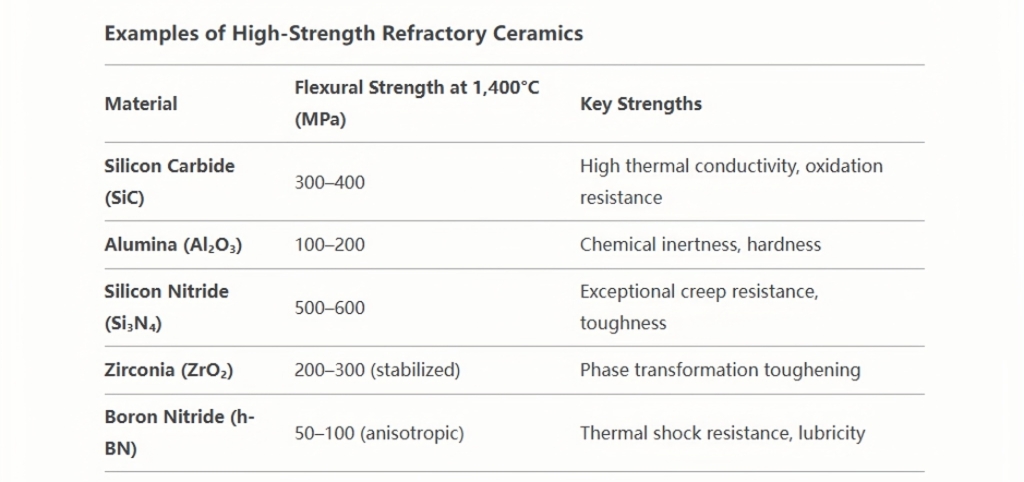
The mechanical strength of refractory ceramics at high temperatures stems from their atomic bonding, microstructure, and innovative composite designs. These materials enable technologies that operate in extreme conditions, from jet engines to nuclear reactors. While challenges like creep and brittleness persist, advances in material science—such as UHTCs and additive manufacturing—are pushing the boundaries of performance. Their ability to combine strength, thermal stability, and corrosion resistance ensures their critical role in advancing industrial efficiency and safety.
Low Thermal Conductivity
Low thermal conductivity is a critical property of many refractory ceramics, enabling their use as insulators in high-temperature environments. Unlike metals, which rely on free electrons for heat transfer, refractory ceramics depend on lattice vibrations (phonons) for thermal transport. Their ability to minimize heat flow makes them indispensable in applications requiring energy efficiency and thermal protection. Below is a detailed analysis of the mechanisms, influencing factors, and industrial relevance of low thermal conductivity in refractory ceramics.
Phonon Scattering Mechanisms:
- Grain Boundaries: Polycrystalline structures (e.g., zirconia, alumina) disrupt phonon propagation, reducing thermal conductivity.
- Defects and Dopants: Impurities (e.g., yttria in stabilized zirconia) and vacancies scatter phonons, lowering heat transfer.
- Amorphous Phases: Glassy regions in ceramics like silica (SiO₂) further impede phonon movement.
Porosity:
- Insulating Gas Pockets: Air-filled pores (common in insulating firebricks) act as thermal barriers, significantly reducing conductivity.
- Trade-offs: High porosity improves insulation but compromises mechanical strength (e.g., lightweight vs. dense refractories).
Crystal Structure Complexity:
- Materials with complex unit cells (e.g., mulite, 3Al₂O₃·2SiO₂) or phase transformations (e.g., monoclinic ↔ tetragonal ZrO₂) hinder phonon transport.
Temperature Dependence:
- Thermal conductivity often decreases at elevated temperatures due to intensified phonon scattering, enhancing insulating performance.
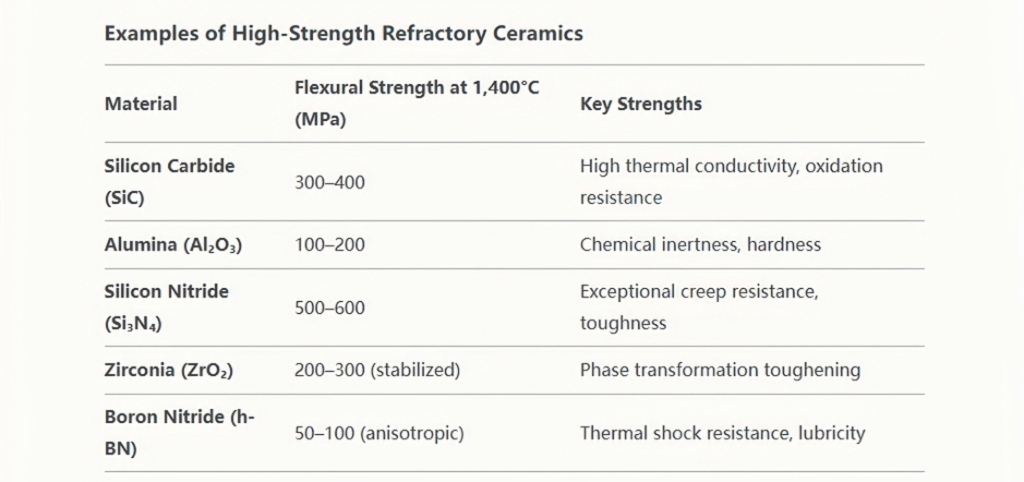
The low thermal conductivity of refractory ceramics arises from phonon scattering, porosity, and complex crystal structures. These materials are vital in industries requiring thermal insulation, from energy-efficient furnaces to aerospace thermal protection systems. While challenges like brittleness and oxidation persist, advancements in nanotechnology and composite design are paving the way for next-generation ceramics that balance insulation, strength, and durability. Their role in sustainable engineering—reducing energy consumption and enabling extreme-environment technologies—underscores their enduring industrial significance.
Controlled Porosity of Refractory ceramics
Controlled porosity is a critical engineered feature of refractory ceramics, balancing thermal insulation, mechanical strength, and chemical resistance. By tailoring pore size, distribution, and volume, these materials achieve optimal performance in extreme environments. Below is a detailed exploration of how porosity is managed and its industrial significance.
Key Methods for Controlling Porosity
- Pore-Forming Agents (Fugitive Materials):
- Materials: Organic (starch, sawdust) or synthetic polymers.
- Process: Burn out during firing, leaving pores. Particle size and distribution dictate pore characteristics.
- Considerations: Decomposition temperature must align with firing cycles to avoid defects.
- Partial Sintering:
- Adjust sintering time/temperature to leave residual pores. Balances strength and porosity but risks under-sintering.
- Foaming Techniques:
- Introduce gas (chemical blowing agents) into slurries to create foam structures. Requires stabilization to prevent collapse.
- Additive Manufacturing (3D Printing):
- Enables precise architectural control of pores (e.g., lattice structures) for tailored thermal/mechanical properties.
- Particle Size Engineering:
- Mixing varied particle sizes influences packing density. Wider distributions can create intentional gaps (pores).
- Post-Processing Leaching:
- Selective removal of soluble phases (e.g., acid leaching) to generate pores. Requires composite raw materials.
Challenges
- Strength-Porosity Trade-off: High porosity reduces mechanical strength; solutions include gradient structures or composites.
- Pore Stability: Sintering at high temperatures may close pores; material selection (e.g., SiC, Al₂O₃) is critical.
- Processing Defects: Rapid burnout of fugitive agents can cause cracking; controlled heating rates are essential.
Material Considerations
- Alumina (Al₂O₃): High melting point; porosity lowers thermal conductivity.
- Silicon Carbide (SiC): Naturally high thermal conductivity; porosity enhances insulation.
- Zirconia (ZrO₂): Phase stability challenges but offers high-temperature resilience.
Conclusion
Controlled porosity in refractory ceramics requires a strategic balance between insulation, strength, and thermal stability. Advances in processing techniques (e.g., 3D printing, optimized sintering) and material science enable tailored solutions for industries demanding high-performance refractories. Future research may focus on hybrid materials and AI-driven pore design to further enhance functionality