Introduction
Textile ceramics refer to ceramic materials processed into fibrous, woven, or textile-like structures. These materials combine the inherent properties of ceramics (e.g., high-temperature resistance, chemical stability) with the flexibility and adaptability of textile forms. Examples include ceramic fibers, woven ceramic fabrics, and 3D-printed ceramic textiles.Textile ceramics, also known as ceramic textiles or ceramic fiber textiles, are advanced materials engineered to combine the intrinsic properties of ceramics with the flexibility and adaptability of textile structures. Their unique characteristics make them indispensable in industries requiring high-performance materials under extreme conditions. Below is a detailed breakdown of their key characteristics:
Characteristics of Textile Ceramics
High-Temperature Resistance
Textile ceramics are renowned for their exceptional ability to withstand extreme temperatures, making them indispensable in industries where conventional materials fail. This property stems from their unique composition, microstructure, and processing methods.
- Operating Range: Textile ceramics can withstand temperatures up to 1600°C–1800°C (depending on composition), far exceeding the limits of most metals and polymers.
- Thermal Stability: Retain structural integrity and dimensional stability even during rapid thermal cycling (e.g., heating and cooling in furnaces or aerospace components).
- Applications:
- Thermal insulation in industrial furnaces, kilns, and reactors.
- Heat shields for rocket nozzles, spacecraft re-entry systems, and hypersonic vehicles.
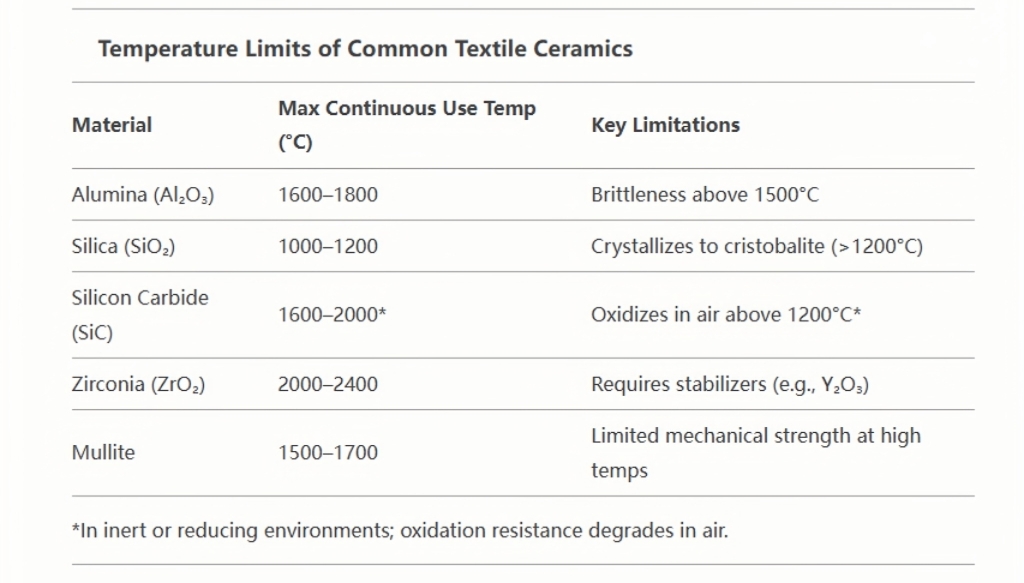
The high-temperature resistance of textile ceramics is a cornerstone of their utility in extreme environments. By leveraging advanced materials science and innovative designs, these textiles push the boundaries of thermal management in aerospace, energy, and industrial applications. Ongoing research aims to address their limitations while unlocking new frontiers in temperature resilience and multifunctionality.
Exceptional Chemical Inertness
Textile ceramics exhibit remarkable chemical inertness, enabling them to resist degradation in corrosive and reactive environments. This property is critical for applications in industries such as chemical processing, energy, and biomedicine.
- Corrosion Resistance: Resistant to acids, alkalis, solvents, and oxidizing agents, making them ideal for corrosive environments (e.g., chemical processing plants).
- Oxidation Resistance: Stable in oxygen-rich or high-temperature oxidative atmospheres, unlike carbon-based materials.
- Applications:
- Linings for pipelines and reactors handling aggressive chemicals.
- Filters for molten metal or exhaust gases in steelmaking.
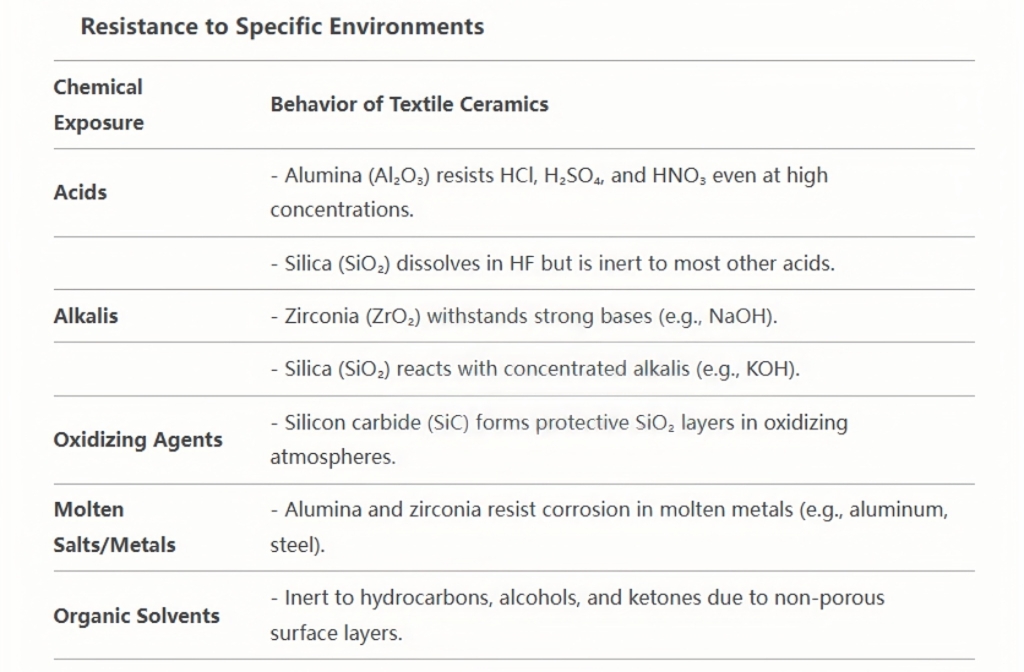
The exceptional chemical inertness of textile ceramics arises from their robust atomic bonding, tailored compositions, and advanced microstructures. This property enables their use in extreme environments—from corrosive industrial processes to biomedical implants—where traditional materials fail. Ongoing innovations in material science aim to address remaining limitations, such as HF vulnerability and recyclability, while expanding their role in sustainable and high-tech applications. By bridging the gap between chemical resilience and mechanical adaptability, textile ceramics continue to redefine material performance in the modern industrial landscape.
Low Thermal Conductivity
Textile ceramics, characterized by their fibrous or woven structures, exhibit low thermal conductivity due to a combination of material properties, microstructural design, and manufacturing processes. This property makes them ideal for high-temperature insulation and other applications requiring thermal management.
- Insulation Efficiency: Textile ceramics exhibit extremely low thermal conductivity (0.1–1.0 W/m·K), minimizing heat transfer and energy loss.
- Mechanism: Achieved through their porous, fibrous structure, which traps air and reduces conductive heat flow.
- Applications:
- Energy-efficient insulation in power plants and industrial boilers.
- Fireproof barriers in buildings and protective gear.
The low thermal conductivity of textile ceramics stems from their unique interplay of material composition, porous microstructure, and phonon-scattering defects. These materials bridge the gap between high-temperature resilience and efficient thermal insulation, driving innovation in industries ranging from aerospace to energy. Ongoing advancements aim to enhance their performance while addressing cost and sustainability challenges.
Lightweight and Low Density
Textile ceramics are engineered to combine the high-performance properties of ceramics with the reduced weight and density of fibrous or woven structures. This unique combination makes them invaluable in industries where minimizing mass is critical.
- Density Range: Typically 0.1–1.0 g/cm³, significantly lighter than bulk ceramics or metals.
- Advantages: Reduces overall system weight, improving fuel efficiency in aerospace and automotive applications.
- Applications:
- Lightweight thermal protection systems (TPS) in satellites and aircraft.
- Composite reinforcements in automotive brake pads.
The lightweight and low-density nature of textile ceramics stems from their porous, fibrous architecture and advanced material engineering. These properties make them indispensable in aerospace, automotive, and energy sectors, where reducing weight directly translates to efficiency gains and cost savings. While challenges like brittleness and high production costs persist, ongoing advancements in nanotechnology and hybrid composites promise to expand their utility, positioning textile ceramics as a cornerstone of next-generation lightweight engineering solutions.
Mechanical Flexibility and Formability
Textile ceramics combine the inherent properties of ceramics (e.g., high-temperature resistance, chemical stability) with the mechanical adaptability of textile structures. Their flexibility and formability enable innovative applications where traditional ceramics fail.
- Textile-Like Behavior: Ceramic fibers can be woven, braided, or knitted into fabrics, felts, or 3D structures.
- Adaptability: Conforms to complex shapes and surfaces, enabling custom designs for niche applications.
- Applications:
- Flexible insulation wraps for irregularly shaped industrial equipment.
- Preforms for ceramic matrix composites (CMCs) in turbine blades.
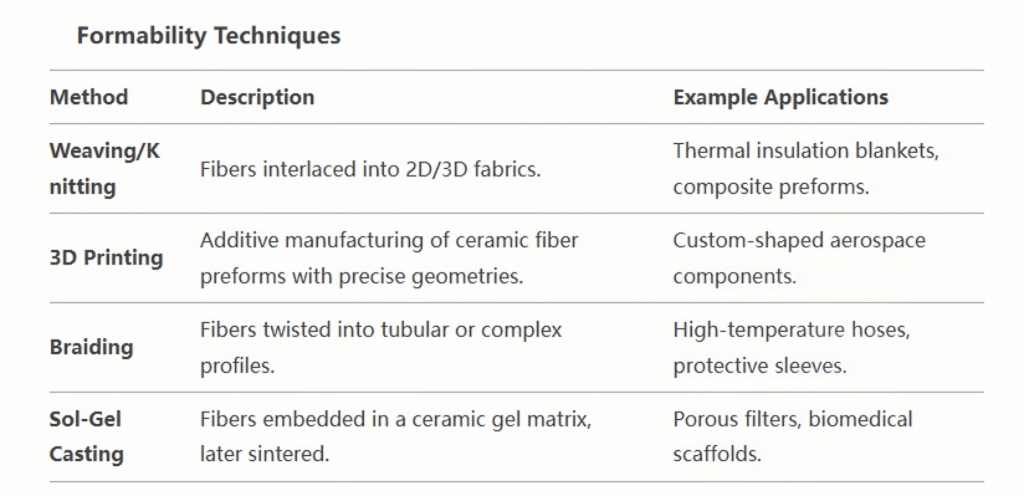
The mechanical flexibility and formability of textile ceramics stem from their unique fibrous architectures and advanced manufacturing techniques. These properties unlock applications in aerospace, energy, and biomedicine, where traditional ceramics are too brittle or rigid. While challenges like sintering control and cost remain,innovations in materials science and digital fabrication promise to expand their role in next-generation engineering solutions.
High Tensile Strength and Durability
Textile ceramics, despite their brittle reputation, exhibit exceptional tensile strength and durability when engineered into fibrous or woven forms. These properties make them indispensable in extreme environments where traditional materials fail.
- Strength-to-Weight Ratio: Ceramic fibers like alumina (Al₂O₃) or silicon carbide (SiC) offer tensile strengths of 1–3 GPa, comparable to steel but at a fraction of the weight.
- Creep Resistance: Maintain performance under prolonged mechanical stress at high temperatures.
- Applications:
- Reinforcement in high-stress components (e.g., jet engine parts).
- Load-bearing structures in extreme environments.
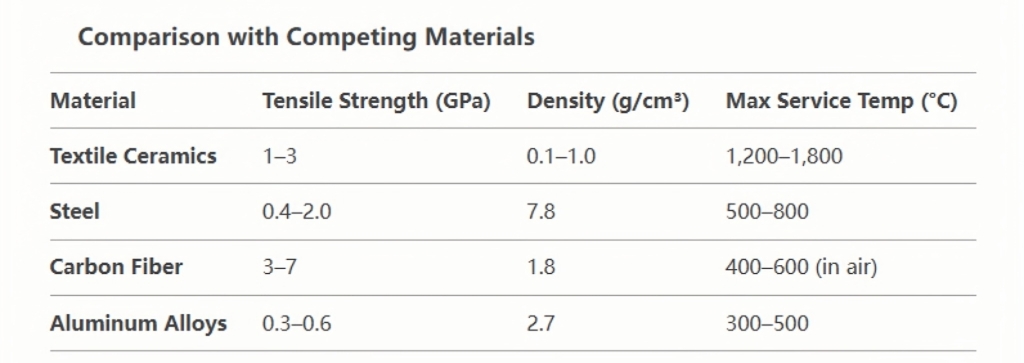
The high tensile strength and durability of textile ceramics stem from advanced material engineering, microstructural control, and innovative manufacturing. These properties enable breakthroughs in aerospace, energy, and automotive industries, where performance under extreme conditions is non-negotiable. While brittleness and cost remain challenges, ongoing research in nanotechnology, hybrid systems, and bio-inspired designs promises to redefine the limits of ceramic resilience, solidifying their role as next-generation engineering materials.
Electrical Insulation
Textile ceramics are exceptional electrical insulators, combining the non-conductive nature of ceramics with the adaptability of textile structures. This property makes them critical in applications requiring electrical isolation in harsh environments.
- Dielectric Properties: Non-conductive even at high temperatures, making them suitable for electrical and electronic systems.
- Applications:
- Insulating layers in high-voltage equipment.
- Substrates for sensors in harsh environments.
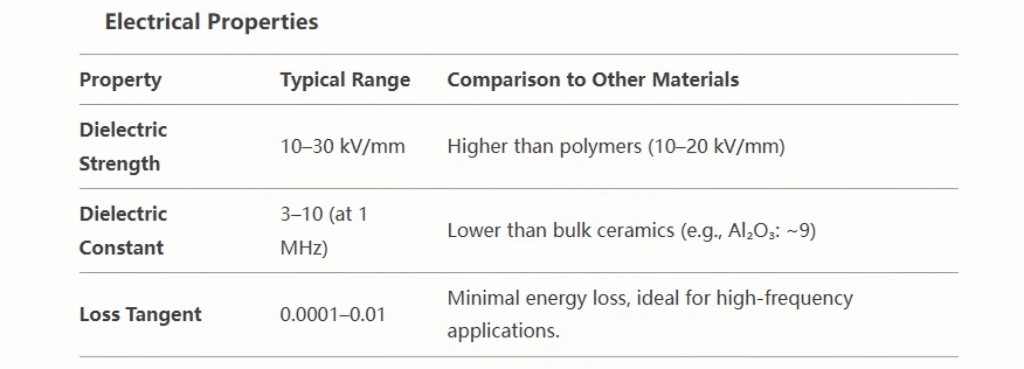
The electrical insulation of textile ceramics arises from their intrinsic non-conductive atomic structure, adaptable microarchitecture, and resistance to extreme environments. These properties make them indispensable in power systems, aerospace, and advanced electronics, where traditional insulators fail under thermal or chemical stress. While challenges like brittleness and contamination sensitivity persist, advancements in hybrid composites and nanotechnology promise to expand their role in next-generation electrical systems, driving innovation in energy efficiency and smart infrastructure.
Environmental Resistance
- UV and Weather Resistance: Stable under prolonged exposure to sunlight, moisture, and weathering.
- Applications:
- Outdoor industrial insulation.
- Protective covers for solar energy systems.
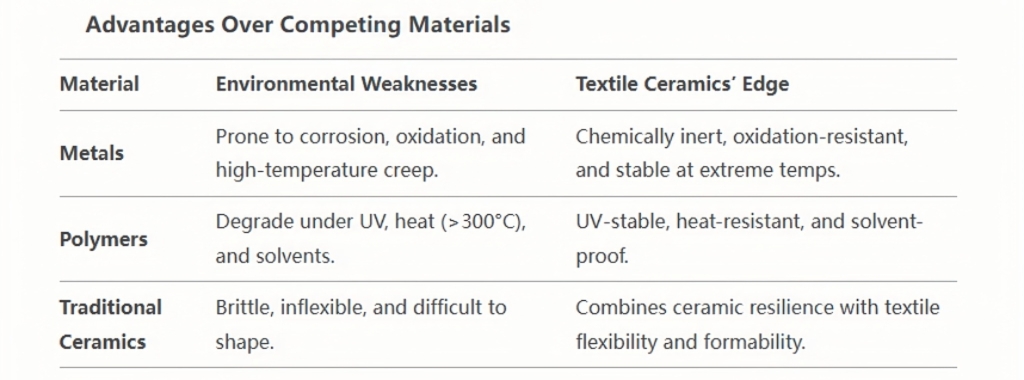
Textile ceramics excel in environments where heat, corrosion, radiation, or mechanical wear would destroy conventional materials. Their unique blend of ceramic durability and textile adaptability makes them indispensable in industries ranging from nuclear energy to aerospace. While challenges like brittleness and cost persist, advancements in composites, surface engineering, and sustainable manufacturing are expanding their role in addressing global environmental and industrial challenges. As industries prioritize resilience and sustainability, textile ceramics are poised to become cornerstone materials for next-generation infrastructure and technology.
Advantages Over Traditional Materials
- Versatility: Combines rigidity of ceramics with textile adaptability.
- Energy Efficiency: Reduces heat loss in industrial processes.
- Longevity: Resists degradation in extreme environments, lowering replacement costs.
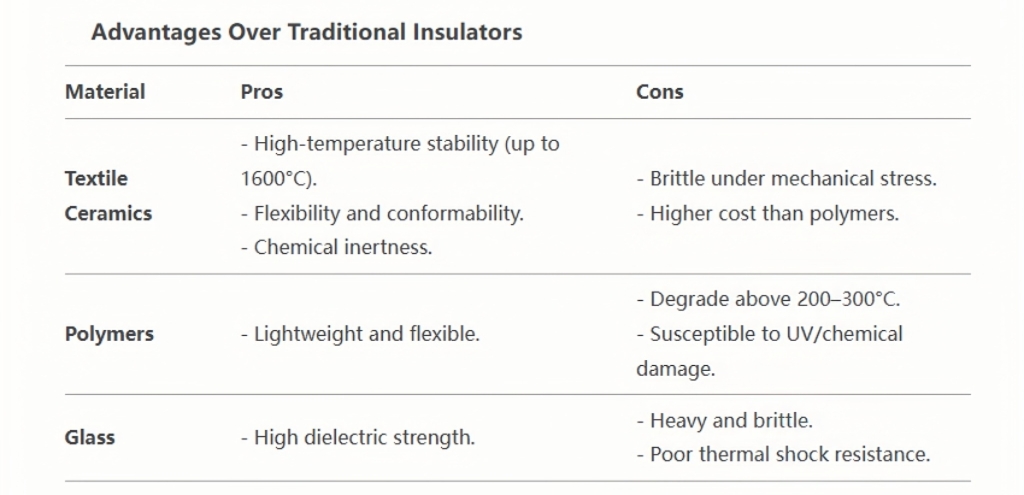
Conclusion
Textile ceramics are a revolutionary class of materials that merge the robustness of ceramics with the versatility of textiles. Their high-temperature resilience, chemical inertness, lightweight nature, and adaptability position them as critical solutions for industries ranging from aerospace to energy. Ongoing advancements in nanotechnology and additive manufacturing (e.g., 3D-printed ceramic textiles) promise to further expand their capabilities, addressing current limitations and unlocking new applications in sustainable engineering and smart materials.